This Fake Skin Allows Prosthetic Hands To Feel Heat, Humidity, And Pressure
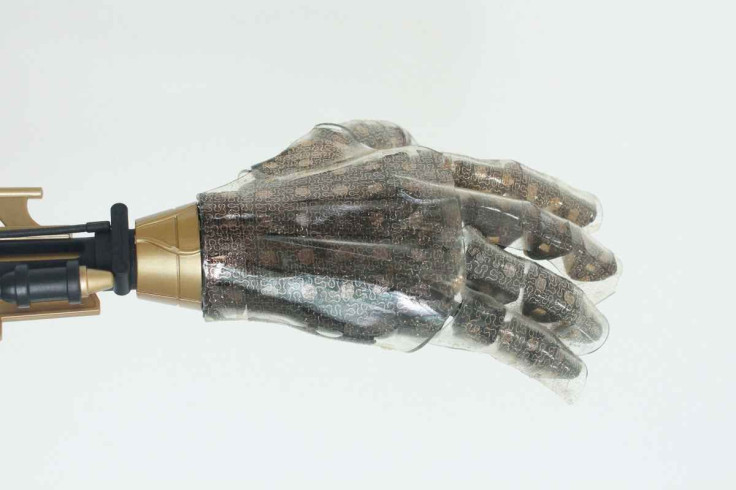
Amputees may soon be able to feel and touch things again even without their limb: scientists have developed artificial skin that is able to detect pressure, temperature, and humidity, making prosthetic limbs far more realistic than in the past.
Currently, certain prosthetic limbs are able to be controlled by an amputee’s thoughts, which is quite remarkable in itself. But the artificial skin may be the next step in making a prosthetic truly an extension of the body. The stretchy material the researchers created, which acts as the “skin,” even has a built-in heater to make it feel like real flesh. Ultimately, the researchers hope, the fake skin will be able to interlock with the patient’s nerves so they can feel what it touches.
“The prosthetic hand and laminated electronic skin could encounter many complex operations such as hand shaking, keyboard tapping, ball grasping, holding a cup of hot or cold drink, touching dry or wet surfaces and human to human contact,” the authors wrote in their study, which was published in Nature Communications.
The artificial skin was developed using a silicone material that is stretchy and transparent. It’s called polydimethylsilozane (PDMS), and it contains silicon nanoribbons that are able to generate electricity when they’re touched or stretched — and are able to detect whether something is warm or cold. In order to test the humidity sensors in the skin, which were able to distinguish between wet and dry, the researchers had the prosthetic hand touch a variety of wet and dry diapers. It was able to successfully sense whether they were wet or dry — something that might prove useful in the future for busy parents.
The researchers were smart in the way they designed the skin and how it wraps around the prosthetic hand. For smaller areas that should be highly sensitive, such as the fingertips, they packed the nanoribbons tightly to increase the amount of sensitivity to touch. Around the wrist, which requires more flexibility in movement, the researchers allowed the nanoribbons to loop around and give room for expansion.
Recreating sense of touch for amputees is, in essence, a notion that involves cheating the brain. Dustin Tyler, a bioengineer at Case Western Reserve University and the author of a previous study that examined creating fake touch through prosthetics, led a study that was able to create sensations artificially. “If we get it correct, the brain interprets it that it’s coming from the hand in the first place,” Tyler said. “The brain doesn’t know we cheated it.”
Though researchers like Tyler have developed “feeling” hands in the past, this is the first time using the stretchy material. “Recent efforts to develop smart prosthetics, which exploit rigid and/or semi-flexible pressure, strain and temperature sensors, provide promising routes for sensor-laden bionic systems, but with limited stretchability, detection range and spatio-temporal resolution,” the authors write in the Abstract. “Here we demonstrate smart prosthetic skin instrumented with ultrathin, single crystalline silicon nanoribbon strain, pressure and temperature sensory arrays as well as associated humidity sensors, electroresistive heaters and stretchable multi-electrode arrays for nerve stimulation.”
It will be some time before the researchers are able to create a connection between the prosthetic skin and the brain in order to let amputees themselves feel its sensations. But it provides hope for those who previously could only have a robotic extension as a prosthetic, rather than a sensitive, feeling, and touching one. “This collection of stretchable sensors and actuators facilitate highly localized mechanical and thermal skin-like perception in response to external stimuli, thus providing unique opportunities for emerging classes of prostheses and peripheral nervous system interface technologies,” the authors write.
Source: Kim J, Lee M, Shim H, Ghaffari R, Cho Hye, Son D. "Stretchable silicon nanoribbon electronics for skin prosthesis." Nature Communications, 2014.