New Printing Process Makes Micro-Machines More Biocompatible For Prosthetics
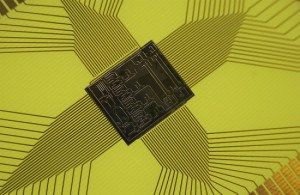
In the cutting-edge fields of microelectronics and nanotechnology, new soft, printable materials in tiny devices “stretch both the imagination and limits of technology,” a new study states.
You’ll find that the implementation of microelectronics is visible in your daily life, most obviously in your smartphone that responds to external stimuli, like movements of your hand.
MEMS, or microelectromechanical systems – sometimes referred to as “micro-machines” – are tiny devices used in consumer electronics like smartphones, automobiles, and medicine. They are created through microfabrication and can range from being simple structures to highly complex electromechanical systems with many moving parts.
They have been used in the past for medical uses, such as developing bionic limbs or prosthetic bladders that respond to and regulate urination for paralyzed people.
Tel Aviv University has developed a new printing process for MEMS components that can boost the efficacy of these MEMS for medical purposes.
With this process, scientists can produce rubbery and paper-thin membranes, creating a kind of organic polymer, which can assist these materials in becoming more biocompatible for medical uses and implantation into the human body. In the past, MEMS components were made primarily from silicon.
Biocompatibility typically refers to the ability of an implant in the human body to not cause toxic changes to biological systems, and instead to exist in harmony with surrounding tissue.
How MEMS Work
When you move your smartphone horizontally to change your screen, for example, MEMS sensors convert movement or chemical signals into electrical signals, orienting the smartphone screen. Other types of MEMS sensors work to convert electrical signals into movement.
While some types of MEMS are simpler than others, the common denominator usually involves some elements with mechanical functionality. Two types of MEMS elements are called microsensors and microactuators. These are considered “transducers,” or devices that can convert energy from one from into another — typically a mechanical signal into an electrical one.
“[T]he printing process may deliver the biggest jolt to the field of medicine,” the report states. Some bionic limbs and prosthetics are made to respond to stimuli from various biological systems, and using MEMS made with polymer membranes could improve their function and safety.
The idea is that these tiny “machines” have the ability to respond to external as well as biological stimuli, improving adaptability to artificial implantations.
Chemical producer Arkema/Piezotech provided the scientists with the polymer for the membranes to give them a chance to test it.
"They just gave us the material and asked us to see what devices we could create with it," said Leeya Engel, an engineering doctoral candidate. "This field is like Legos for grownups."